Estimated reading time: 11 minutes
Table of contents
- Editor’s Note
- Understanding HVACD in Cannabis Grow Facilities
- Key Considerations for HVACD System Design
- Selecting the Right HVACD Equipment
- Air Distribution: A Critical Factor
- Enhancing Energy Efficiency in Cannabis Facilities
- Additional Considerations for HVACD Design
- Final Thoughts
- HVACD Cannabis Grow FAQs
- Additional Resources
- Free eBooks For Cannabis Business Success
- Latest Articles
Cliff Notes: HVAC / HVACD Systems for Cannabis Grow Facilities
Objective: Understanding the critical role of tailored HVACD systems in cannabis cultivation facilities and designing climate-controlled environments that maximize plant health, yield, and operational efficiency.
Key Components:
- HVACD systems are essential for maintaining precise climate control in cannabis grow facilities, directly impacting plant health, yield, and product quality.
- Early planning with cultivators determines system needs, including lighting setup, plant density, and ideal temperature/humidity ranges.
- Heat load management is critical in sealed grow environments where lighting and dehumidification equipment generate substantial internal heat.
- Purpose-built HVACD systems outperform standard units, offering full air recirculation, tight humidity control, and contamination prevention.
- System configurations vary by facility size and needs, including DX cooling with reheat, chilled water systems, and water-cooled heat pumps.
- Effective air distribution prevents mold and stress, utilizing ducted systems, circulation fans, and destratification techniques for even airflow.
- Energy efficiency and air quality can be optimized through smart controls, sustainable technologies (like heat recovery), MERV/HEPA filters, and condensate reuse.
Partner with Catalyst BC to design and implement high-performance HVACD systems that meet the rigorous demands of modern cannabis cultivation. Our team combines technical expertise with industry insight to create efficient, compliant, and scalable climate solutions. Contact us for a Complimentary Consultation.
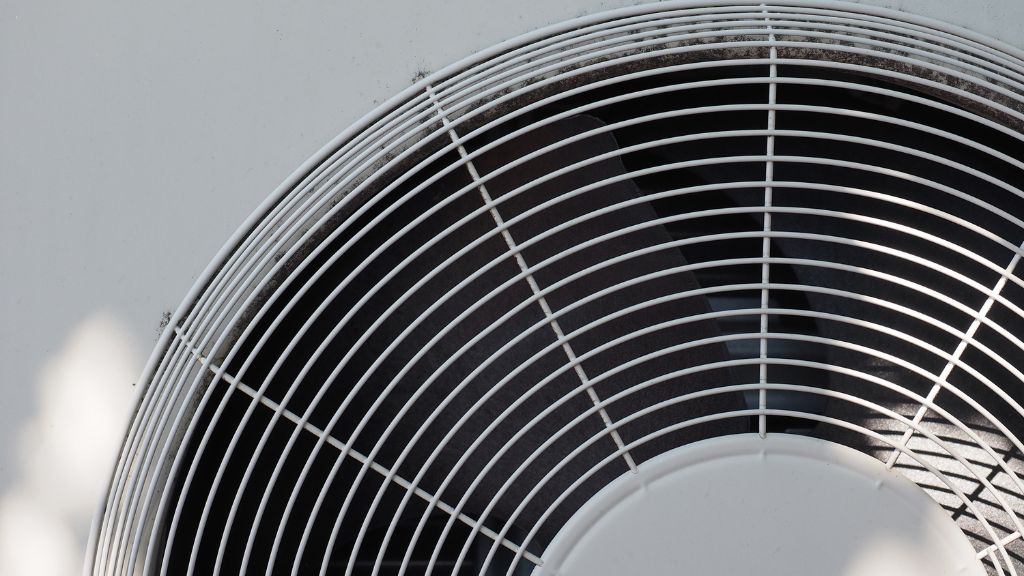
Editor’s Note
This article is part two of the Cannabis Facility Design Essentials series. Find the additional parts below:
1. Cannabis Grow Facility Design: Essential Considerations for Success
2. Demystifying HVACD Systems for Cannabis Grow Facilities
3. Optimizing Water Use in Cannabis Grow Facility Design
4. Cannabis Facility Design Safety: Creating Compliant Environments
Understanding HVACD in Cannabis Grow Facilities
Cannabis grow rooms require precisely controlled environments, making Heating, Ventilation, Air Conditioning, and Dehumidification (HVACD) systems essential for success. As plants progress through their growth cycle—transitioning from the Veg room to the Flower room—environmental factors such as lighting, irrigation, temperature, and humidity must be carefully managed to achieve optimal yields and product quality. Many cultivation businesses seek guidance from a Cannabis Consultant to ensure their HVACD systems are designed to meet both efficiency and regulatory standards.
Key Considerations for HVACD System Design
A well-planned HVACD system starts with a thorough discussion with the cultivation team and a Cannabis Consulting expert to determine the ideal system configuration. Important factors include:
- Grow Lights – Quantity, type, wattage, and lighting schedule.
- Plant Volume and Watering Needs – The number of plants and irrigation rates, or canopy area with estimated water usage.
- Temperature and Humidity Targets – Day and night settings for optimal plant growth.
- Harvesting Methods – Understanding drying and curing needs to maintain efficiency.
Because most cannabis grow rooms follow a “box inside a box” construction model, external heat loss is minimal. Instead, HVACD systems must manage the heat produced by grow lights and internal equipment, such as dehumidifiers and circulation fans. Working with an experienced Cannabis Consultant can help cultivators navigate these challenges while maintaining compliance with state and local regulations.
Managing Latent and Sensible Cooling Loads
Latent cooling load primarily stems from plant transpiration—the process where water moves from roots to leaves and is released as vapor. The rate of transpiration depends on light levels, airflow, temperature, and humidity.
A key metric in environmental control is Vapor Pressure Deficit (VPD), which measures the difference between moisture levels inside plant leaves and the surrounding air. VPD influences transpiration rates and overall plant health, making it an important consideration for HVACD system design. Many growers rely on Cannabis Consulting services to fine-tune VPD settings and optimize plant growth conditions.
Selecting the Right HVACD Equipment
HVACD systems must be capable of maintaining precise temperature and humidity levels while ensuring continuous airflow. Since cannabis facilities typically recirculate 100% of their air to preserve CO₂ enrichment and prevent contamination, properly sized equipment is critical.
Many facilities dedicate a separate air handling unit for each grow room, ensuring maximum environmental control and preventing cross-contamination. Earlier attempts to use standard residential or commercial HVAC systems often resulted in humidity control failures and equipment inefficiencies, leading to the rise of purpose-built HVACD solutions tailored to the unique demands of cannabis cultivation. Engaging a Cannabis Consulting firm early in the process can prevent costly mistakes and ensure seamless system integration.
Common HVACD System Configurations
Several HVACD system types are commonly used in cannabis grow rooms, including:
- Packaged Air Handling Units with Direct Expansion (DX) Cooling – Often supplemented with ceiling-mounted dehumidifiers.
- Water-Cooled Heat Pumps – Can reject heat to a geothermal loop or fluid cooler, often requiring additional dehumidification.
- DX Cooling with Hot Gas Reheat – Provides low dewpoint dehumidification, reducing or eliminating the need for supplemental dehumidifiers.
- Chilled Water Systems with Reheat – Frequently used in large-scale facilities for enhanced efficiency and control.
Since no single system fits all cannabis grow rooms, designers must balance installation costs, operating expenses, construction timelines, equipment lead times, geographic climate considerations, and energy efficiency when making selections. Many operators turn to Cannabis Consulting services to determine the best system for their facility’s unique requirements.
Air Distribution: A Critical Factor
While selecting the right HVACD equipment is crucial, air distribution within the grow room is equally important. Poor circulation can lead to stagnant zones, increasing the risk of mold and plant stress.
For optimal plant growth, a constant air velocity should be maintained at the canopy level, using:
- Ducted Airflow from HVACD Equipment – Ensures even temperature and humidity distribution.
- Circulation Fans – Helps eliminate microclimates and promotes even transpiration.
- In-Rack Airflow Systems – Essential for multi-tiered Veg rooms.
- Destratification Fans – Useful for maintaining uniform air movement.
Ductwork placement must be carefully planned alongside lighting, fire protection, plant racks, and fertigation piping to avoid obstructions. Many facilities use fabric ductwork, which is lighter, customizable, and easier to clean compared to traditional sheet metal ducts. Cannabis Consulting professionals can help design an air distribution strategy that maximizes efficiency and plant health.
Enhancing Energy Efficiency in Cannabis Facilities
Indoor cannabis cultivation is highly energy-intensive, often requiring up to 80 watts per square foot, with half of that attributed to HVACD equipment. Energy-efficient solutions include:
- Integral Energy Recovery Devices – Featured in some air-handling units.
- Heat Recovery Chillers – Used in chilled water systems for improved efficiency.
- Geothermal Solutions – Viable for certain facility locations.
- Automation and Controls – Advanced controls optimize HVACD performance by synchronizing with lighting and irrigation systems.
Facility owners can benchmark energy usage to track efficiency improvements over time. Organizations like the Resource Innovation Institute provide valuable guidelines for optimizing energy and water consumption in controlled environment agriculture. A Cannabis Consultant can help growers implement the best energy-efficient HVACD strategies tailored to their facility.
Additional Considerations for HVACD Design
Filtration & Air Quality
HVACD systems should incorporate MERV 13 or higher filters to maintain air quality and protect equipment. Some facilities opt for HEPA filtration for even greater air purity.
Disinfection & Contaminant Control
To prevent mold and pathogens, growers may use:
- Ultraviolet (UV) Lamps – Installed in air-handling systems.
- Photocatalytic Oxidation – Used for air purification.
- Thermal Disinfection – Some growers disable HVACD systems and increase room temperatures above 125°F between harvests to kill contaminants.
Odor Control & CO₂ Enrichment
Cannabis facilities must comply with odor mitigation regulations, often using carbon filters in exhaust systems. Additionally, CO₂ enrichment requires constant monitoring to prevent unsafe gas concentrations.
Condensate Management & Humidification
Grow rooms produce significant condensate from cooling and dehumidifier coils, which can be collected and treated for reuse in irrigation. Conversely, humidification may be necessary in Veg rooms, where lower transpiration rates can result in excessively dry air.
Advanced HVACD Controls
Integrating HVACD controls with lighting, irrigation, and fertigation systems enhances environmental stability and plant health. Smart automation systems enable real-time monitoring and adjustments, optimizing both energy efficiency and cultivation outcomes.
Final Thoughts
Designing an effective HVACD system for a cannabis grow facility requires careful planning, precise equipment selection, and thoughtful air distribution strategies. By incorporating energy-efficient technologies, advanced filtration, and climate automation, cultivators can create an optimal environment for plant growth while maximizing operational efficiency.
Partner with Catalyst BC to design and implement high-performance HVACD systems that meet the rigorous demands of modern cannabis cultivation. Our team combines technical expertise with industry insight to create efficient, compliant, and scalable climate solutions. Contact us for a Complimentary Consultation.
HVACD Cannabis Grow FAQs
HVACD (Heating, Ventilation, Air Conditioning, and Dehumidification) is critical in cannabis grow facilities to maintain precise temperature, humidity, and air quality. Proper grow room ventilation ensures optimal plant health, reduces mold risk, and enhances yield quality.
Unlike standard HVAC systems, HVACD cannabis systems are designed to handle high humidity, intense lighting, and CO₂ enrichment while preventing contamination. These systems integrate cannabis cultivation climate control with specialized dehumidification and airflow solutions. Cannabis Consulting professionals can help design an air distribution strategy tailored to your specific needs.
Key factors include grow room ventilation, lighting type and placement, plant canopy size, irrigation rates, airflow distribution, and energy efficiency. A well-balanced HVAC cannabis system helps optimize plant transpiration and environmental stability.
Proper grow room air circulation prevents stagnant air, mold growth, and uneven temperature distribution. Controlled air exchange for cannabis regulates humidity, enhances CO₂ absorption, and supports uniform plant development.
Common HVAC solutions for grow rooms include packaged air handling units with dehumidifiers, chilled water systems, DX cooling with reheat, and water-cooled heat pumps. Each system is selected based on facility size, climate, and energy efficiency goals.
VPD measures the difference between moisture inside plant leaves and surrounding air, influencing transpiration rates. A well-calibrated HVAC cannabis system maintains an optimal VPD range to maximize plant growth and nutrient uptake.
Multi-level cultivation requires specialized airflow solutions, in-rack ventilation, and zoned dehumidification to maintain consistent conditions across all tiers. Controlled air exchange for cannabis ensures proper airflow distribution. Multi-level cultivation demands precision in HVACD for proper usage. It’s highly recommended to work with a professional cannabis consulting team for multi-tier grow rooms.
Even airflow prevents microclimates, reduces disease risk, and ensures consistent humidity control. Techniques like ducted air distribution, circulation fans, and in-rack airflow improve grow room air circulation for healthy plant development.
Dehumidifiers and HVACD-integrated humidity controls remove excess moisture from plant transpiration, reducing the risk of powdery mildew and botrytis. Controlled environment HVACD systems prevent over-saturation of indoor air.
Using integral energy recovery devices, geothermal cooling, heat recovery chillers, and advanced automation minimizes energy waste. Benchmarking energy use helps optimize indoor grow facility HVAC performance while reducing operational costs. A professional cannabis consultant can help determine the most energy-efficient strategy based on your cultivation facility.
HVAC cannabis systems must balance airflow and CO₂ supplementation. Since most grow rooms operate with 100% air recirculation, precise ventilation ensures CO₂ levels remain optimal without excessive loss.
MERV 13 or higher filters are recommended to capture airborne particles, preventing contamination. Some cannabis HVAC systems also use HEPA filtration and UV disinfection for additional air purity.
Activated carbon filters, negative pressure systems, and sealed ductwork help contain cannabis odors. HVAC solutions for grow rooms integrate odor mitigation to comply with regulatory requirements.
Excess condensate from cooling coils can be collected, filtered, and reused for irrigation, reducing water waste. HVAC cannabis solutions often incorporate condensate reclamation systems for sustainability.
Automated HVAC cannabis systems integrate with lighting, irrigation, and fertigation to dynamically adjust temperature and humidity. Smart monitoring ensures cannabis cultivation climate control is optimized for energy efficiency and plant health.
Additional Resources
Free eBooks For Cannabis Business Success
Latest Articles
- Utah Medical Cannabis Pharmacy License Applications Open for 2025: Eligibility, Deadlines, and RequirementsThe Utah Department of Agriculture and Food (UDAF) has officially launched the first application period for two independent medical cannabis pharmacy licenses, running from July 1 through July 31, 2025. Originating from House Bill 54, passed during Utah’s 2025 legislative session, these new pharmacy licenses aim to broaden medical cannabis access in medically underserved areas across the state.
- Cannabis Startup Costs: From Licensing to ProfitabilityStarting a legal cannabis business isn’t just about getting a license—it’s about building a profitable, compliant, and sustainable operation in one of the world’s most capital-intensive and regulated industries. Many entrepreneurs enter this space with many goals, good intentions, and passion, but ultimately fail because they underestimate the cost, complexity, experience, and time required to turn a cannabis license into a thriving business.
- Cannabis License Pitfalls: How to Avoid Common Cannabis Licensing MistakesAs new adult-use programs launch, many entrepreneurs are eager to start growing, processing, or selling cannabis. Excitement runs high, but the industry’s heavy regulations and complex operations can quickly overwhelm even experienced business owners. Common mistakes include underestimating compliance requirements, rushing facility design, skipping proper procedures, and more.
- Maximizing Your Minnesota Cannabis Microbusiness or Mezzobusiness LicenseMinnesota’s new adult-use cannabis law allows microbusinesses (one store, up to 5,000 sq ft indoor, ½ acre outdoor) and mezzobusinesses (up to 3 stores, 15,000 sq ft indoor, 1 acre outdoor) to cultivate, manufacture, sell, and transport cannabis under one license. These vertically integrated licenses offer flexibility, but also come with complex state rules.
- The Recipe for a Top-Tier Cannabis DispensaryOperating a highly reviewed, top-performing cannabis dispensary takes more than simply stocking product and unlocking the doors. It requires operational discipline, regulatory expertise, top-tier customer service, dynamic merchandising, and a culture of accountability and community. With the cannabis industry continuing to expand—and regulations constantly evolving—success is defined by how seamlessly a dispensary integrates compliance, product curation, staff training, and marketing into day-to-day operations.
- Minnesota Lottery Results: June 5 Cannabis License Drawings and What’s NextThe Minnesota Lottery for cannabis business licenses reached a pivotal milestone on June 5, as the Office of Cannabis Management (OCM) conducted randomized drawings for select license types. These lotteries were open to both social equity applicants and general applicants vying for limited licenses to operate as cultivators, manufacturers, and mezzobusinesses. Additionally, a separate lottery was held exclusively for social equity applicants seeking a retail cannabis license.