Cannabis production strategies may differ from one facility to another, but most facilities share a common goal: to produce the highest quality product at the lowest cost. One area of the cultivation cycle that is often overlooked but has great potential for optimization is the drying and curing process.
Many cultivators use bins or totes to harvest, weigh, and transfer cannabis plants to the drying room. The plants are then manually hung one by one on wire, pipe, hangers, hooks, and/or racking.
Once the product has been dried it is then manually unhung plant by plant and placed back into the bins or totes. These are then transferred to trimmers to process into the finished product. These transfer events have significant labor costs and more importantly, can reduce quality by degrading trichomes and associated cannabinoid and terpene content.
In lean farming and manufacturing, we refer to these actions as non-value-adding touch points. The process outlined above is not only cost-intensive for the producer but also one that reduces quality and value to the end consumer, who should be at the center of every decision a cannabis producer makes.
Let’s take a look at two options that allow operators to reduce labor and associated costs while producing a higher quality product. Below, we introduce you to drying carts and drying rack solutions for your operation.
First thing’s first: Ditch the Bins
Many growers use plastic bins or totes to help them harvest. An inexpensive and simple solution, binning plants has been a common method amongst growers.
Unfortunately, it greatly increases labor requirements due to the many staff and non-value-adding touch points with the plants. These touch points also negatively impact the final quality of the product as the terpenes and trichomes are disturbed each time.
Bins or totes also present additional and unnecessary cross-contamination, workflow, and labor challenges. They need to be cleaned and sanitized after each batch or during daily use. Many facilities are not set up or staffed appropriately to properly clean and sanitize bins and totes regularly.
In addition, bins and totes take up a tremendous amount of space, which is often not taken into consideration during the facility design process. They are often stacked or nested one on top of another. If these bins are not cleaned and have been dragged on the floor, operators risk contaminating their cannabis plants and dried flowers that come in contact with the inside of the bins.
Labor is the biggest cost for a cultivation operation. And as it so happens, the harvest and post-harvest team is often the largest department by headcount.
By introducing equipment such as drying carts or racks, operators can decrease their labor costs while increasing product quality, all without the use of bins or totes.
Optimize Your Drying Process
The first step in optimizing your drying process is to evaluate the space in your facility. There are two unique solutions to meet cultivators’ drying needs: mobile drying carts and mobile drying storage racks.
An easy way to tell them apart is to remember this: drying carts bring work to the workers while drying racks bring workers to the work.
Drying carts are mobile by design. Staff roll the drying carts into the flowering room being harvested and hang plants directly on the drying carts without the need for hangers or hooks.
The drying carts are then transferred to the drying room. Once the plants have dried, the carts are then rolled into the trimming room. The product moves efficiently around the facility with little to no touching of the actual plants.
Drying racks differ in that staff must still bring plants to the racks where they manually hang from the rack. A mobile drying cart can still be used for the transfer to eliminate the use of bins or totes. However, what sets these drying racks apart from common drying setups is that the racks can span the full height of the room, taking advantage of not only the total available square feet but cubic feet as well.
There are pros and cons to both options. Ultimately, your operation’s capacity, efficiency, and labor demands will be the deciding factor.
Space Requirements
If space is not an issue, the ideal choice is drying carts for the points mentioned above: lower labor costs and higher quality product. The carts must be stored when not in use, and you’ll also need adequate space in your flower room for the carts to roll through the aisles. We recommend a minimum of 28” width aisles.
If you’re already tight on space in the drying rooms and are using trellis or cable wire, installing mobile drying racks will greatly optimize your room’s plant-drying capacity. Drying racks can help transform a tight, restricted space into an efficient one that supports your scaling business.
To get an idea of how much space is required for either racks or carts, we crunched some numbers for you below. Here, you can see how much square footage of drying space is required for each equipment option.
For this example, let’s consider 1000 harvested cannabis plants. The following space is required in your drying area for each solution (the range accounts for plant size and density):
- 2-tier drying carts: 300-600 sq. ft.
- 3-tier drying carts: 200-400 sq. ft.
- Mobile drying racks (4 tiers): 200-400 sq. ft.
You can see that the available space in the facility is the main consideration here. Let’s take a deeper dive into the pros and cons of drying racks vs drying carts.
Drying Carts
The Pros
- Ideal for purpose-built cultivation facilities that can dictate the size of the drying rooms
- No ladders or lifts required
- Drying carts have options for two or three levels of cantilever-style finger hooks, which eliminate the need to use hooks, zip ties, coat hangers
- Improves operational workflow by reducing non-value adding plant touches
- Improves trichome and terpene preservation by eliminating non-value-adding touchpoints
- Eliminates the use of bins/totes
- Brings the work to the workers
- Plants can be defoliated on drying carts if desired
- Less expensive than investing in drying racks
- Anti-fungal/bacterial coating option
- Easy to clean and sanitize
- Reduces labor to clean and sanitize drying rooms as room can be cleared of carts and equipment
The Cons
- Drying carts do not maximize cubic or square feet when compared to mobile drying racks.
- Drying carts that do not nest, break down easily with minimal tools
- Can be challenging to create linear queues in drying rooms
- Increased risk for finger and hand injuries
Drying Racks
The Pros
- Drying racks are ideal for:
- Existing cultivation facilities with suboptimal-sized drying rooms looking to retrofit
- New facilities that undersized their drying room and need to maximize every cubic foot
- Pre-operational facilities that are in the design phase and need to free up space for other areas of the design
- Typical racking height up to 16′ with 6 tiers
- Typical racking width options: 24″, 36″, 48″
- Drying racks support multiple hanging options from hang bars that allow for the use of hooks and coat/plant hangers, wire grid, and finger hooks
- The most efficient solution to maximize square and cubic feet
- Ability to scale by adding tiers based on phases or increased yields
- Anti-fungal/bacterial coating option
The Cons
- Requires lift or ladder to hang as well as take down
- More touchpoints, which lead to the degradation of THC and terpenes
- Higher labor cost
- Less efficient to clean and sanitize, compared to drying carts
Now that you’ve made it this far, you’re probably getting a good idea of which option (drying racks or carts) might work best for your growing space.
Michael is the Director of Cultivation at Pipp Horticulture as well as the Chief Operating Officer of Catalyst BC and has consulted on numerous cannabis cultivation facilities.
Additional Resources
Consulting Services For Cannabis, Hemp, Psilocybin, and Natural Medicine
- Consulting Services Overview
- Business Strategy
- Financial Planning
- Cannabis, Hemp, Psilocybin, & Natural Medicine Licensing and Applications
- Facility Design
- StartUp Support
- Genetic Development
- Business Turnaround
- Operational Optimization
- Vertical Farming
- Controlled Environmental Agriculture (CEA)
- State and Country Services Directory
- Blog
- Home
Testimonials and Public Relations
Latest Articles
- Utah Medical Cannabis Pharmacy License Applications Open for 2025: Eligibility, Deadlines, and RequirementsThe Utah Department of Agriculture and Food (UDAF) has officially launched the first application period for two independent medical cannabis pharmacy licenses, running from July 1 through July 31, 2025. Originating from House Bill 54, passed during Utah’s 2025 legislative session, these new pharmacy licenses aim to broaden medical cannabis access in medically underserved areas across the state.
- Cannabis Startup Costs: From Licensing to ProfitabilityStarting a legal cannabis business isn’t just about getting a license—it’s about building a profitable, compliant, and sustainable operation in one of the world’s most capital-intensive and regulated industries. Many entrepreneurs enter this space with many goals, good intentions, and passion, but ultimately fail because they underestimate the cost, complexity, experience, and time required to turn a cannabis license into a thriving business.
- Cannabis License Pitfalls: How to Avoid Common Cannabis Licensing MistakesAs new adult-use programs launch, many entrepreneurs are eager to start growing, processing, or selling cannabis. Excitement runs high, but the industry’s heavy regulations and complex operations can quickly overwhelm even experienced business owners. Common mistakes include underestimating compliance requirements, rushing facility design, skipping proper procedures, and more.
- Maximizing Your Minnesota Cannabis Microbusiness or Mezzobusiness LicenseMinnesota’s new adult-use cannabis law allows microbusinesses (one store, up to 5,000 sq ft indoor, ½ acre outdoor) and mezzobusinesses (up to 3 stores, 15,000 sq ft indoor, 1 acre outdoor) to cultivate, manufacture, sell, and transport cannabis under one license. These vertically integrated licenses offer flexibility, but also come with complex state rules.
- The Recipe for a Top-Tier Cannabis DispensaryOperating a highly reviewed, top-performing cannabis dispensary takes more than simply stocking product and unlocking the doors. It requires operational discipline, regulatory expertise, top-tier customer service, dynamic merchandising, and a culture of accountability and community. With the cannabis industry continuing to expand—and regulations constantly evolving—success is defined by how seamlessly a dispensary integrates compliance, product curation, staff training, and marketing into day-to-day operations.
- Minnesota Lottery Results: June 5 Cannabis License Drawings and What’s NextThe Minnesota Lottery for cannabis business licenses reached a pivotal milestone on June 5, as the Office of Cannabis Management (OCM) conducted randomized drawings for select license types. These lotteries were open to both social equity applicants and general applicants vying for limited licenses to operate as cultivators, manufacturers, and mezzobusinesses. Additionally, a separate lottery was held exclusively for social equity applicants seeking a retail cannabis license.
Explore Our Articles
Business Funding cannabis applications Cannabis Bar Cannabis Business Optmization Cannabis Business Services cannabis careers Cannabis Compliance Cannabis Consumption Cannabis Consumption Bar Cannabis Inventory Management Systems Cannabis Investors cannabis jobs Cannabis Legalization cannabis licensing Cannabis Lounge cannabis marketing Cannabis Operational Procedures cannabis outreach Cannabis Regulations Cannabis Security Cannabis Software Cannabis Startup Cannabis Supply Chain Cannabis Technology Colorado controlled environment agriculture Cultivation cultivation facility Dispensary Design facility design Financial Planning Legal Update Legislation Medical Cannabis Minnesota Natural Medicine Nebraska New York Odor Control Oregon Psilocybin Psychedelics Recreational Cannabis Solventless Extraction Tribal Cannabis Licensing
Free Ebook – Start Your Own Legal Cannabis Business
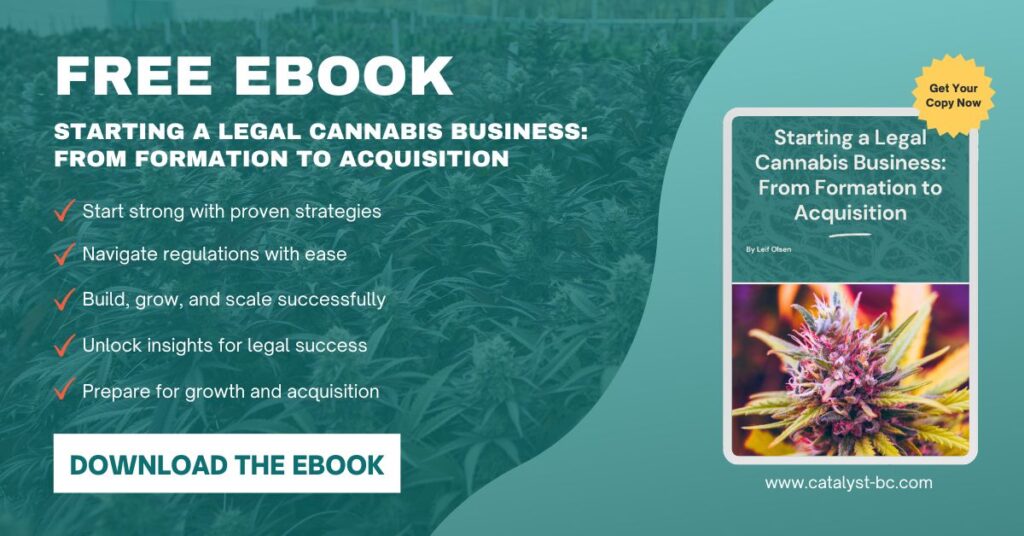